MIG vs TIG Welding: Which Should You Learn First for DIY Projects?
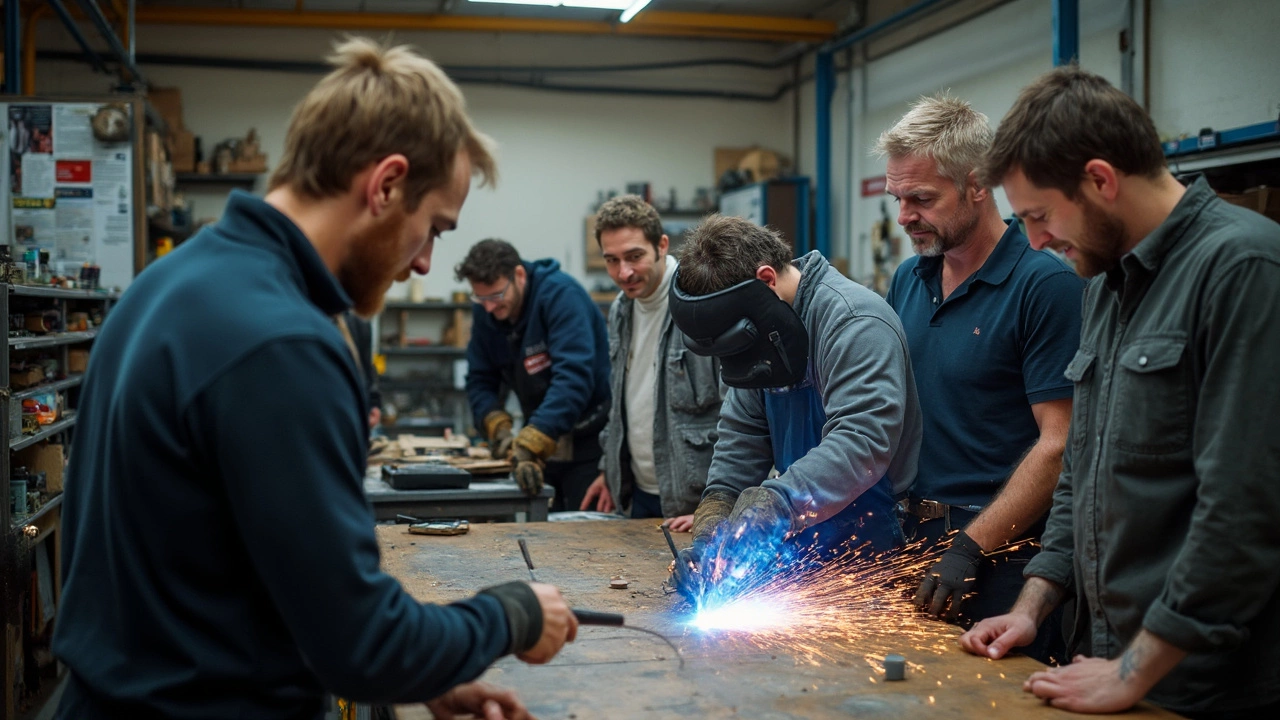
If you’re standing in your garage, staring at a heap of metal scraps and a bright red welder you barely know how to turn on, you’re not alone. Loads of people wrestle with the same head-scratcher: do you take the plunge into MIG or TIG welding first? There’s this gritty romance to welding—just ask anyone who has ever fixed an old bike frame or made wild garden sculptures. But the tools you pick now will shape the jobs you can tackle, how fast you learn, and even how many times you’ll burn holes through your workbench. Let’s get real about what makes each method tick and which path is worth staking your free weekends on.
What Sets MIG and TIG Welding Apart?
Alright, both MIG (Metal Inert Gas) and TIG (Tungsten Inert Gas) welding fuse metal using electric arcs. But from there, the details couldn’t be more different. When you think about MIG, picture a trigger-happy setup. You squeeze the trigger, feed wire automatically, gas shields your weld, and you’re off to the races. It’s almost like using a glue gun for metal. MIG’s forgiving if your hands aren’t surgeon-steady, and you can get those classic weld beads on everything from lawn mower repairs to heavy-duty steel gates. TIG, on the other hand, is a craft. You’re handling a torch in one hand and feeding a rod with the other, all while managing a foot pedal if you’re really in the weeds. It’s a three-part dance—torch, rod, and pedal—for welding purists chasing the cleanest, prettiest seams imaginable.
Why choose one over the other? MIG is fast. Seriously fast. Want to get through thicker metal, lay down long, even beads, or bang out projects without spending ten weekends learning technique? MIG’s your mate. TIG’s slower, but man, does it shine on tricky metals like aluminium and stainless steel. It lets you control heat, depth, bead shape—basically the fine-tuning that makes project cars or metal art happen. Now, here’s an interesting stat: According to The Fabricator, 60% of beginner welders in the UK pick MIG to start with, simply because it helps them knock together practical projects almost straight away.
TIG does have its moments of glory. Talk about razor-thin materials or delicate work, and TIG is king. You won’t get those burnt holes you see when you try patching up a rusty exhaust with MIG. But there’s a catch—TIG makes your clumsy first attempts glaringly obvious. Your hands, your patience, and even your eyesight face the ultimate test. It’s not just a physical thing, either. TIG expects you to pay attention to gas flow, electrode angle, puddle shape—there’s real pride in nailing it, but it takes time. As the American Welding Society puts it:
"TIG requires more practice and patience, but it develops a welder’s finesse like nothing else."
Cost-wise, get ready for sticker shock. A basic MIG welder kit (gas and all) often comes in under a grand here in Bristol—sometimes less if you score used. TIG is a pricier investment, with the machine, foot pedal, and various bits easily pushing your total past £1,200. And that’s before you start buying specialty electrodes or rarefied tungsten rods. The learning curve hits your wallet before it hits your skillset.
Feature | MIG Welding | TIG Welding |
---|---|---|
Ease of Use | Beginner-friendly | Challenging |
Project Speed | Fast | Slow |
Metal Types | Steel, Aluminum (with special wire) | Steel, Aluminum, Stainless Steel |
Best For | Thick materials, big jobs | Precision, thin metals |
Equipment Cost | £400 - £1,000 | £800 - £1,500 |
PPE Needed | Standard gloves, helmet | Same + better eye protection |
Here’s a tip for folks around Bristol: Our damp weather plays havoc with gas flow and weld quality. Stick to wind shelters or tight garages, especially if you’re still learning gas control. And don’t cheap out on wire and rods—quality makes a huge difference, especially when beads refuse to flow or stick. If you ever smell a whiff of burning plastic, check your technique instead of blaming your gear. Bad hand placement and angle are learning curve rites of passage, trust me.
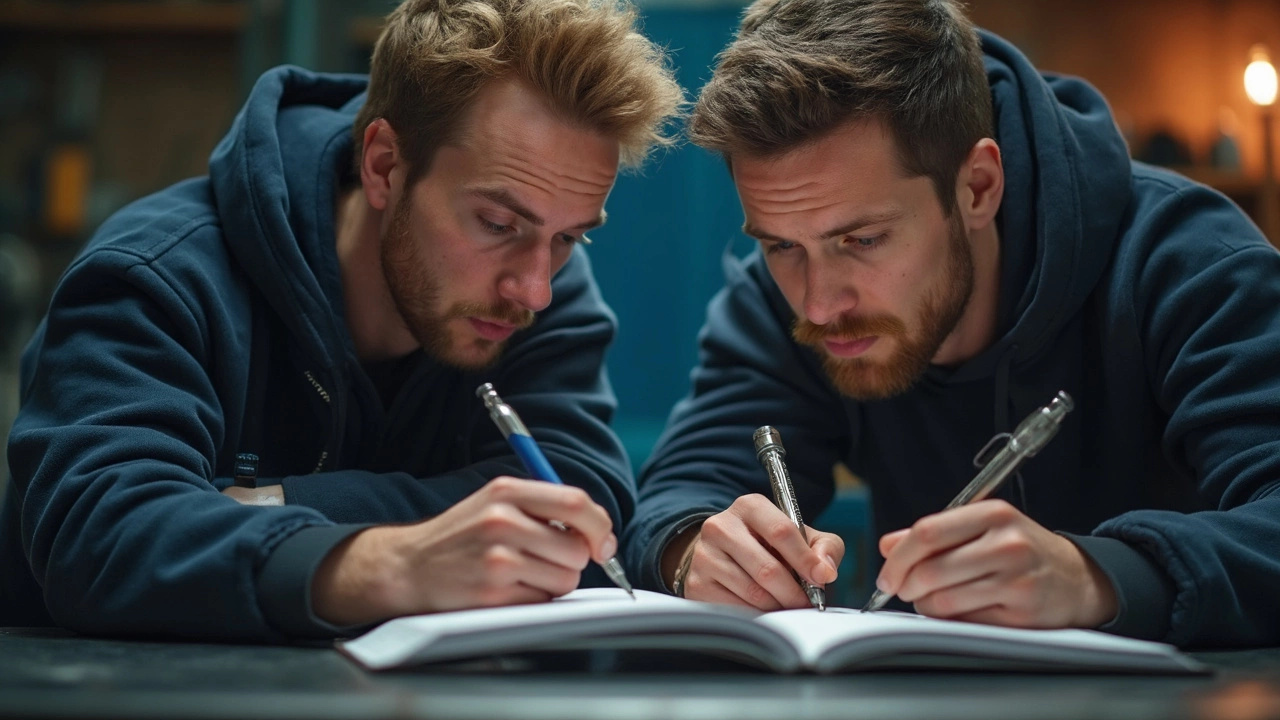
How Beginners Can Make the Right Choice
The first real question you should ask isn’t which method is cooler, but what you want to weld. Are you fixing up a Land Rover, patching shed doors, or going for showpiece furniture? Start by listing five realistic projects you’d feel good about finishing this year. If four of those are heavy steel or car repairs, then MIG welding should top your shortlist. It’s forgiving of rookie errors. You can get a working joint with shaky hands—honestly, the trickiest part is not running out of patience after your fifth ugly bead.
How about folks itching to weld up lightweight racks, custom brackets, or do artistry on bikes or small engines? TIG wins. It’s the go-to when you want clean seams on pipes, intricate curves, or neat joints where looks matter. Keep in mind, though, that every beautiful TIG weld seen on cars and coffee tables hides endless hours spent practising torch angles and beads on scrap metal. That patience builds real skill, but it isn’t for the halfhearted.
Worried about having no mentor? MIG learning resources flood YouTube and hobbyist forums. It’s easier to get fast feedback, easier to get replacement parts, and easier to join a local welding club where someone has probably made every rookie mistake you’re about to make. For TIG, you might find yourself squinting at your third hand and wondering why the puddle runs away from you. Side note: most trade schools in England start students on MIG for the first semester, then introduce TIG. That pathway works—and the numbers show it. According to City & Guilds data, 73% of Level 2 welding students report higher confidence using MIG after the first ten weeks. Confidence leads to practice; practice leads to better welds, no matter your path.
Here’s an insider’s trick: buy quality gloves. Seriously. You’ll want the thin, heat-resistant kind for TIG, not those clunky leather mitts that come cheap in hardware store packs. And invest in a helmet with a good auto-darkening filter—protect your eyes from arc flash, even if you think you’re just "testing" settings for a second. Never weld without covering up, as skin burns are common even before you master technique. My pal in the local Bristol classic car club still wears the evidence of his early days—sunburned wrists from reaching too far under fenders. Learn from his mistakes, save your skin.
Want to stretch your pounds? Buy a used MIG welder with enough amperage for 6mm steel, not the lowest-power model on the shelf. Newer welders (especially inverter types) are smaller and more portable, perfect for home garages, but don’t be afraid of older gear in good nick. And don’t forget about fume extraction—MIG can churn out more nasty smoke than you expect if you’re welding anything coated or painted, especially indoors.
If you still can’t decide, here’s a fun weekend experiment: grab a mate who already welds, try both techniques side by side. You’ll know in half an hour if the TIG torch’s elegance wins you over or if you fancy the grunt and speed of MIG’s wire feed. Not everybody’s hands or temperament suits every tool. Plenty of seasoned welders bounce between both processes depending on the task. That flexibility sometimes matters more than masterful technique. The important thing isn’t perfection—it’s progress and not giving up after the first few disasters.
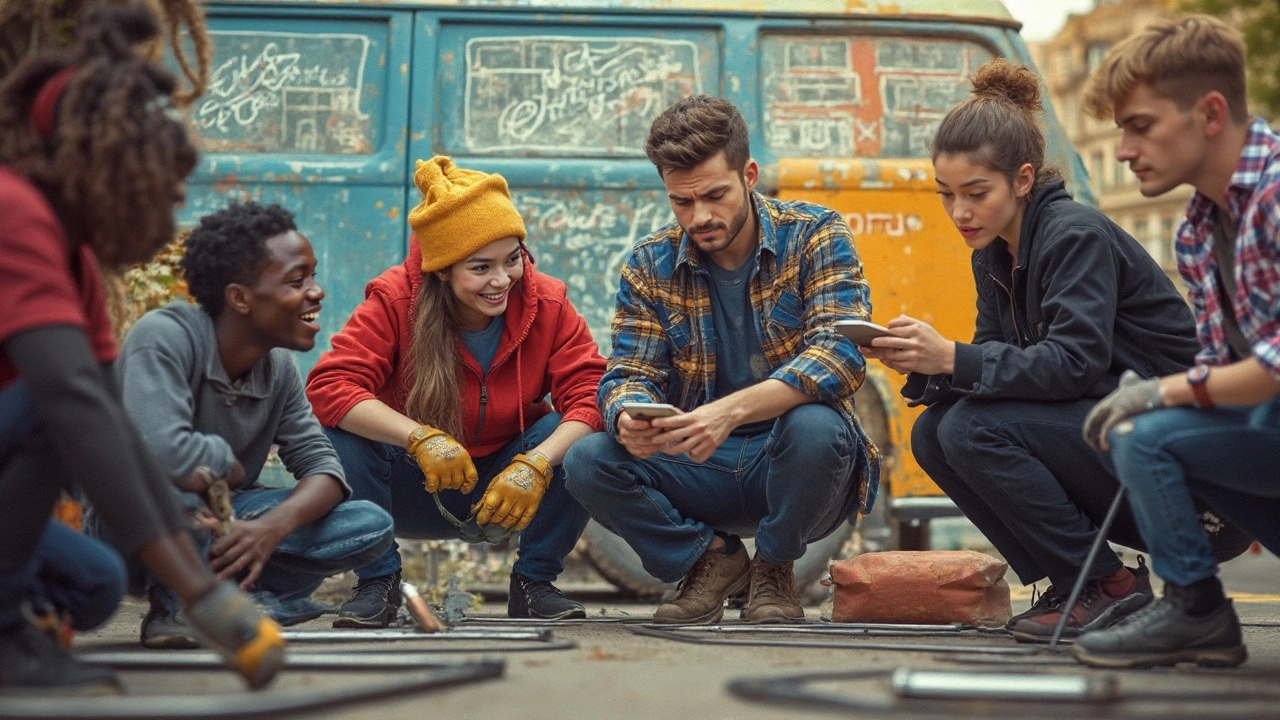
From First Weld to Serious Projects: Tips That Make You Better, Faster
No matter which welding process you fall for, the real learning happens after you spark up that first arc and start melting metal (and maybe your nerves). Expect ugly beads, spatter, and the odd burn. The only folks with perfect welds on day one are either liars or hiding decades of practice. But there are hacks, hard-won from garages across England, that will get you up to speed and keep your projects from landing in the scrap bin.
First, scrap metal is your best friend. Don’t shell out on new steel until your beads don’t look like bird droppings. Practice lap joints, T-joints, and fillet welds on old car panels or shelves. The muscle memory from hours of "just another bead" pays off when you move to live projects. Next, control your positioning—pull a proper stool up so your elbow rests steady, especially for TIG. People forget that fatigue ruins more welds than impatience. And tilt your head so you can see into the puddle; welding blind is hobbyist purgatory.
If you make a mess, don’t panic. Every pro welder I’ve met in Bristol can tell stories of early beads that looked like chocolate bars dragged over concrete. Consistency is king—fiddle with your settings, track what works, and photograph your progress. In fact, a 2022 survey by Welders’ Digest found that welders who tracked setting and bead photos improved twice as fast as those who just winged it. Give it a try—even your failures can be catalogued into wins over time.
Another thing: quick and proper prep beats high-end gear every time. Clean your metal. Burn off rust and paint with a wire brush or grinder first. Shiny surfaces give your welds a fighting chance. And always clamp firmly—jumping or warped pieces cause more rookie misery than cheap tools. A wise old timer at the Bristol Metalworkers Society once said,
"A clean joint and a steady hand will cover more mistakes than a fancy welder could hide."
Upgrading tools is cool, but pointless if you run before you walk. Stick with recommend gas mixtures—CO2/argon blends for MIG, pure argon for TIG. If you’re welding aluminium, make sure your MIG has a spool gun or prepare to pony up for AC TIG capacity; aluminium punishes the unprepared. Here’s a quick cheat sheet for those new to welding aluminium:
- Use clean, dedicated brushes for aluminium only.
- Double-check your wire type: ER4043 or ER5356 are common for MIG.
- Increase your travel speed to avoid burning through.
- Argon only for shielding—MIG mixes won’t work right.
- Practice on scraps until your beads lose that stubborn black soot.
Look out for local Bristol trade shops and markets—some run beginner welding courses and have kit rentals. Even shadowing a pro for a day can save weeks of YouTube trial and error. Sometimes watching how experts set up and tackle tricky repairs gives you the shortcut you desperately need.
Finally, never stop asking for help. Welding forums, subreddit groups, even in-person clubs can offer the best tips. Got a picture of a broken weld or a weird problem? Post it. Most welders are a friendly bunch who remember being hopeless with wobbly torch hands and fried circuits. Progress comes faster when you share the journey, good and bad. Whether you try MIG or TIG first, commit to seeing it through beyond the first pile of failed beads—and you’ll be bragging about your metalwork in no time.
Write a comment