Challenges Faced in a Welding Career: Insights from Experts
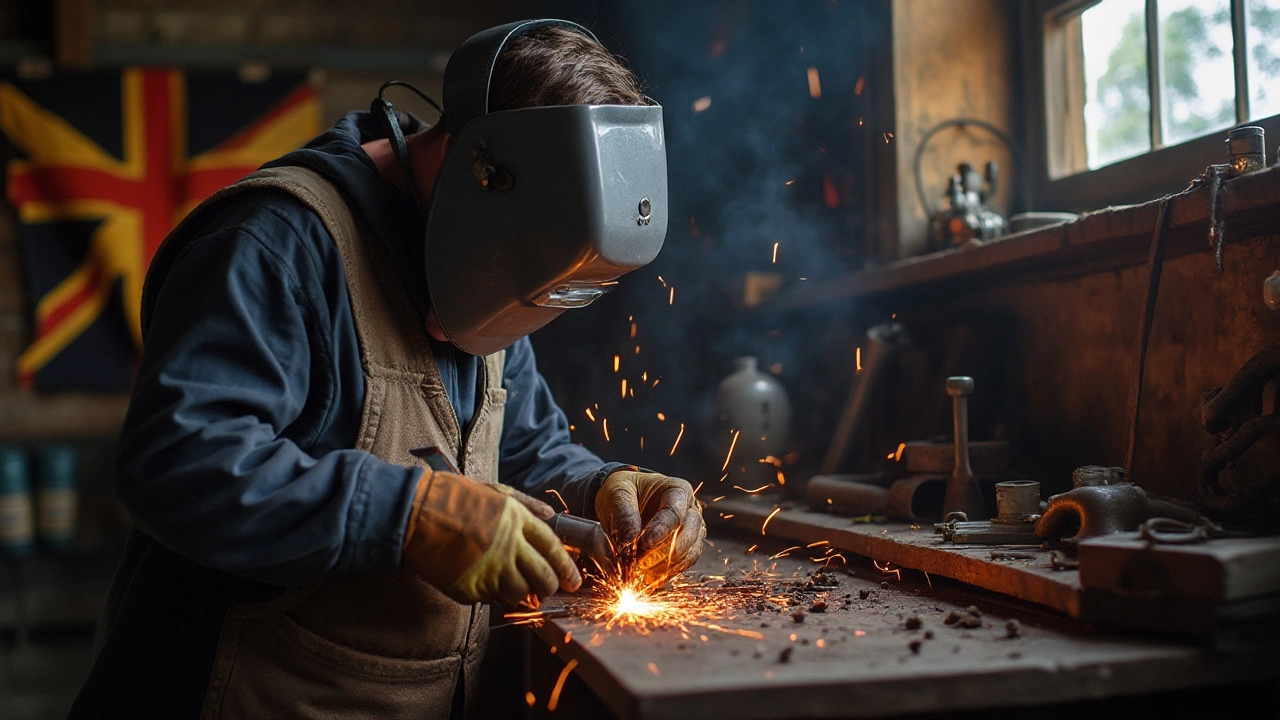
Welding might seem like just connecting pieces of metal, but let's not underestimate the skill and dedication it involves. The life of a welder is filled with challenges that test both the body and mind. With a spark here and a flash there, the untrained eye might only see sparks flying, but there's so much more going on.
The workday begins, often in cramped conditions or outdoors braving the elements. Each weld tells a story of craftsmanship and precision, making it a career that requires continual learning and adaptation. As you dive into this article, you'll discover what makes welding one of the most demanding yet rewarding professions out there. Stay with us as we explore the trials and triumphs of a welding career.
- Physical Demands of Welding
- Mastering Technical Skills
- Safety Challenges and Precautions
- Environmental Factors Affecting Welders
- Understanding Various Welding Techniques
- Tips for Aspiring Welders
Physical Demands of Welding
In the welders’ world, the job is not just about joining metals; it's a rigorous test against one's physical endurance. Welding can be exceptionally taxing, with long hours spent in uncomfortable positions. Imagine crouching, kneeling, and sometimes lying down, all while maintaining a steady hand and keen eye on the molten weld pool. The level of physicality involved is often underestimated, but it plays a crucial role in everyday tasks. Welders must also carry heavy equipment and materials, adding strain to the body, more so when there are multiple shifts involved. This constant need for physical exertion can lead to muscle strain, reinforcing the need for regular fitness and stretching routines for those in this trade.
The nature of welding also requires keen attention to detail and dexterity, especially for intricate welds. Workers not only face the challenge of staying physically fit but must also combat the fatigue that comes with the intense focus required during welding. It’s not just muscles and bones that bear the load; the mind, too, is continuously challenged. Occupational safety standards try to mitigate risks, but the job's inherent demands keep welders on their toes. A successful welder needs a blend of physical strength and mental stamina, balancing the requirements of quality work and health.
"Welding is as much about mental strength as it is about physical endurance" - An old adage shared among veteran welders often rings true, emphasizing the need for both body and mind fitness.
Sweating under a protective helmet and suit can also intensify the feeling of physical pressure due to heat exposure. Heavy welding gear, worn to protect from splashes and burns, can cause discomfort over prolonged periods. The heat generated not only comes from the welding process itself but potentially the job's environment. Welders working outdoors are subject to weather swings from bitter cold to scorching heat, raising the demands on the body.
With such physical demands, taking care of one’s body becomes paramount. Strategies like maintaining proper hydration, using ergonomic tools, and engaging in strength-building exercises can help greatly. Nutrition cannot be overlooked either, as a balanced diet fuels the intense energy requirements this work demands. Knowing how to lift correctly and employing safety harnesses and supports in dynamic environments can prevent injury.
A study on welder health reported that back pain and shoulder discomfort were the most common complaints among professionals. To counteract such issues, welders are advised to take regular breaks and adjust their working positions whenever possible. Their personal and professional lives intertwine, often requiring welders to have a support system that encourages a balanced lifestyle. This includes understanding the physical ramifications of the career and the potential need for long-term care if injuries are sustained.
While welding might seem daunting due to these physical demands, it also offers a great sense of accomplishment. Seeing a completed, functional piece that once began as separate parts is rewarding. This pride in one's work drives welders to push through the physical challenges, learning to embrace a tough job that requires true grit and determination.
Mastering Technical Skills
In the world of welding courses, mastering technical skills is more than a necessity—it's the backbone of a welder's career. From understanding the science behind molten metals to the precise execution of welding techniques, the technical complexity never ceases to amaze those new to the field. Among the key skills, the mastery of different welding processes such as MIG (Metal Inert Gas), TIG (Tungsten Inert Gas), and Stick welding stand paramount. Each method requires a unique approach and an understanding of its best application scenario—a realm where textbook knowledge meets hands-on experience. Take MIG welding, for instance. Known for its speed and versatility, it allows quick welds on various materials but demands a proper understanding of heat settings and wire feed rates to optimize results.
The beauty of welding is that no single project is ever the same. A seasoned welder learns to adapt, analyzing materials to choose the optimal method. For TIG welding, often revered for its finesse, welders must master the art of controlling the torch and filler rod simultaneously. "TIG welding is like playing the piano," as one veteran welder eloquently noted. It requires precision and patience. The right hand steadies the torch like pressing piano keys, while the left feeds the filler rod like creating rhythm and harmony, a dance of skill and timing.
Technical understanding becomes even more crucial with complex welding positions. Fieldwork often demands overhead or vertical welding, a task that requires dexterity and an understanding of gravitational impacts on molten pools. Welding positions are as vital as the type of welds themselves. Courses often begin with the basics like flat and horizontal welds, progressing to the more challenging positions such as vertical and overhead. Mastery involves understanding the physics behind each movement, while also predicting the flow of molten metal—a skill that's honed with time and practice.
A commitment to continuous learning is essential, especially with technological advancements impacting the field. Recent developments in automation and robotics are reshaping the landscape, but this doesn't edge out the need for a human touch. Instead, it places strong emphasis on upskilling and adaptation. Welders find themselves learning about operating robotic welders alongside traditional methods, a harmonious blend of new and old. As technology evolves, courses increasingly incorporate these advances, preparing welders for future demands. "The technology we choose has to work for us," says a respected industry leader, stressing on balancing technological adoption with core skills.
Welding skills aren't solely about creating a perfect seam; they involve understanding material properties too. Different metals react differently under heat stress, and knowing these characteristics can make or break a project. Metals like aluminum and stainless steel have precise handling requirements, influencing factors such as heat input and protection gas choices. This technical acumen is often what separates novice welders from their expert counterparts.
Finally, mastering these technical nuances is a journey where there is always something new to learn. As you navigate the intricacies of a welding career, remember that each spark ignites innovation. Our fellow welders are more than just metalsmiths; they are artists of precision and adaptability. And that, in essence, is the true heart of mastering the technical skills needed in welding.
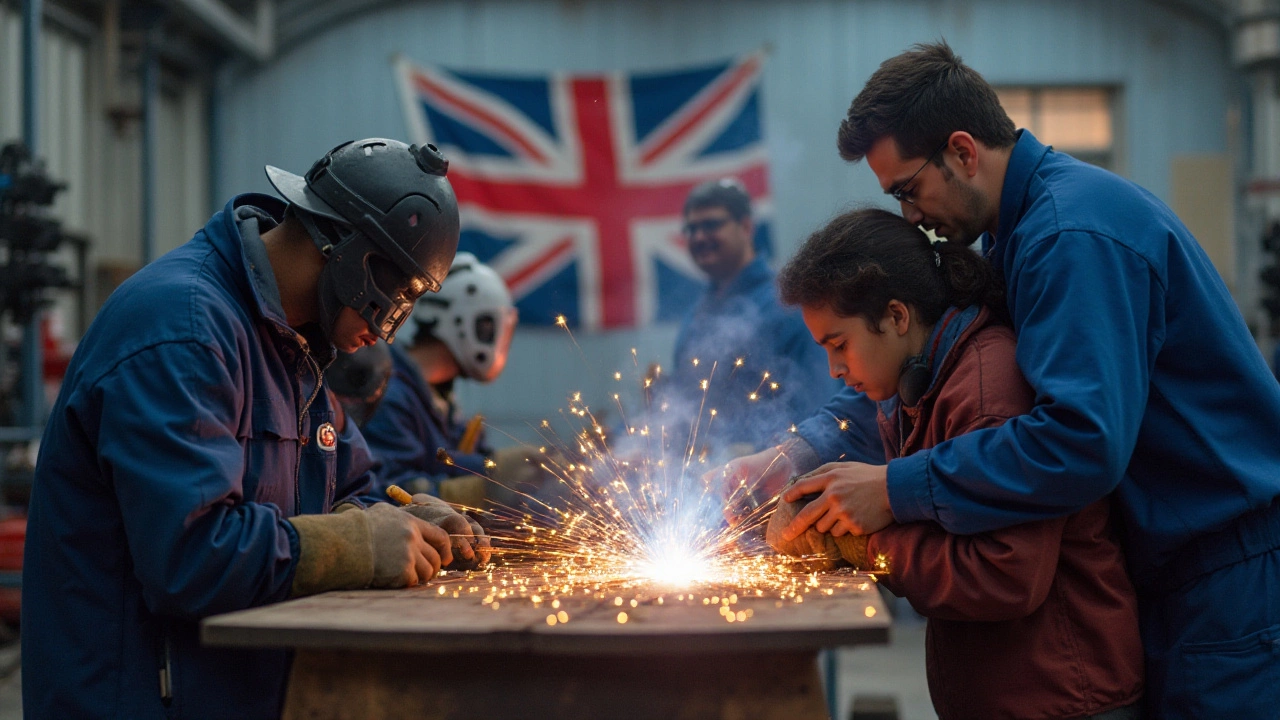
Safety Challenges and Precautions
Welding is often celebrated for its dynamic, craft-like quality, but with it comes a legion of safety challenges that every professional welder must overcome. Given the powerful tools and materials involved, safety is paramount. From blinding sparks to dangerous fumes, welder faces multiple hazards that demand vigilant safety measures. Starting with the basic requirement—protective gear. Welders suit up with helmets, gloves, and gear tailored to fend off the harmful effects of ultraviolet and infrared lights that are part of the welding arc's stunning display. There's an understanding among welders that these safeguards aren't just accessories but vital necessities.
The environment where welders ply their trade is just as crucial as the tools employed. Adequately ventilated spaces are non-negotiable to prevent the inhalation of fumes that can lead to severe respiratory issues over time. Safety isn't a one-size-fits-all solution. Each specific welding technique, such as MIG or TIG, carries its unique hazards, requiring specific approaches. On a humid or rainy day, imagine handling equipment that conducts electricity—conditions must be carefully controlled to mitigate electrical shock risk.
Integrating a culture of safety in the workplace is key to fostering an atmosphere where every team member takes accountability for their actions. Daily safety check-ins and comprehensive training on the latest safety standards and technologies are essential practices in the field. According to the Occupational Safety and Health Administration (OSHA), "Preventative measures and adherence to regulations are critical for reducing workplace incidents." Establishing a robust safety protocol isn't just about compliance—it's a commitment to the well-being of each team member.
Given the diversity of environments where welders operate, including construction sites, factories, or shipyards, understanding each location's specific safety parameters aids in developing appropriate precautions. For example, in enclosed spaces, the risk of fume accumulation is significantly higher. Welders are advised to use forced ventilation systems or wear respirators as an additional layer of protection. Let's not forget the importance of regular equipment maintenance. A well-maintained piece of machinery is less likely to produce unexpected sparks, minimizing accident risks.
Improving safety in welding isn't just the responsibility of the welder. It requires a collaborative effort between employers, safety officers, and the welders themselves. Implementing safety drills, promoting open communication for reporting hazards, and encouraging an ongoing dialogue about safety improvements forms a robust framework for minimizing risks. And while it may seem like welding is a daunting career when factoring in these challenges, it's these operational paradigms and precautions that protect welders and allow them to refine their expertise safely.
Environmental Factors Affecting Welders
Welders often work in environments that most people would find quite challenging. Whether it's the searing heat of a summer day or the biting cold of winter, these hardworking professionals are expected to perform their duties without a hitch. The climate isn't just a backdrop—it's an influential factor that can affect welding quality and safety. Extreme temperatures can impact the welder's concentration and physical condition, potentially increasing the risk of errors or accidents. For instance, working in intense heat without proper hydration could lead to heat exhaustion, which severely affects judgment and motor skills.
The workplace itself also plays a critical role. Many welding jobs are located in confined spaces that, without adequate ventilation, can become a suffocating atmosphere. The lack of proper airflow means that toxic fumes from certain types of metals or coatings can quickly accumulate, posing a health hazard. It's not just the air that's a concern; the surfaces welders work on can become dangerously hot or cold, leading to the risk of burns or frostbite. Protecting oneself requires understanding the environment and using the right protective equipment, like respirators and specialized clothing.
Noise is another underestimated aspect of the environment that welders have to contend with. A welder is often surrounded by the constant clatter of industrial machinery, which can be deafening. Prolonged exposure to high noise levels can lead to hearing damage, underscoring the importance of wearing the correct protective gear, such as earplugs or noise-canceling headphones. Let's not forget the impact of inadequate lighting, especially in poorly lit industrial settings, which can strain the eyes and increase the likelihood of mistakes.
"In welding, your environment can be as much of a challenge as the task itself," says Henry Lee, a seasoned welding instructor. "Understanding and preparing for these elements is key to not only completing a job effectively but also maintaining one's health over time."
Finally, let's consider the psychological toll of these environmental factors. Welch welders often share stories of the mental strain caused by continuously adapting to challenging surroundings. This stress is only amplified by the constant awareness of potential hazards around them, leading to both physical fatigue and mental exhaustion.
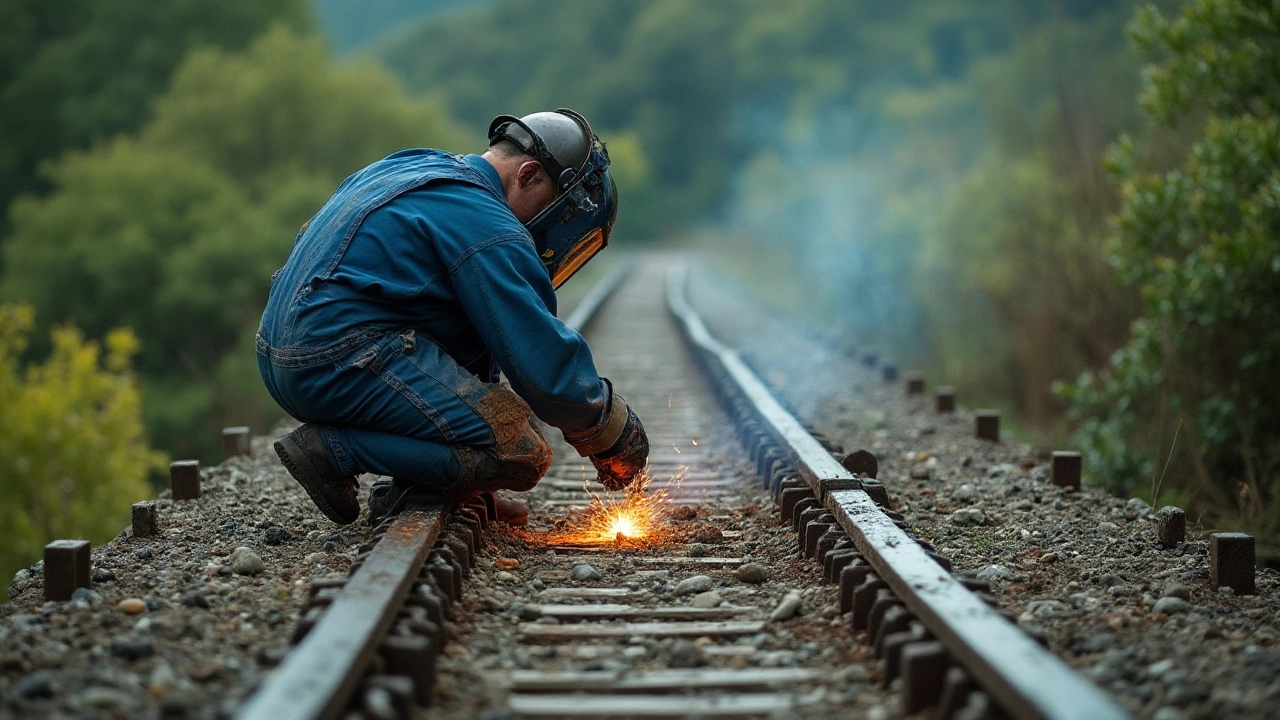
Understanding Various Welding Techniques
Welding is a universe of its own, rich with techniques each crafted for specific purposes and outcomes. At its core, welding courses introduce you to a world where metals are melded into sturdy creations. The roots of welding techniques are diverse, spanning various complexities. Let’s embark on understanding some of the most prevalent techniques in the welding world. Shielded Metal Arc Welding (SMAW), commonly known as stick welding, is among the oldest. It's favored for its simplicity and dependability across different environments. Whether on a construction site or deep in a workshop, SMAW stands its ground. The method relies on an electrode coated in flux to lay the weld, and it's renowned for its adaptability.
Around the corner lies Metal Inert Gas (MIG) welding, also known as Gas Metal Arc Welding (GMAW). This method shines in its ability to produce clean welds, particularly praised in industries where precision and aesthetics are imperative. The process utilizes a wire feeding gun that melts the wire into the joint, seamlessly combining strength with the ease of automation. Professionals accentuate welding skills in these projects often to accommodate the fast-paced demands.
Let’s not forget Tungsten Inert Gas (TIG) welding, revered for precise control and finish. Mastering TIG requires finesse and patience, earning its place as a go-to in sectors craving exquisite craftsmanship—think aerospace and automotive industries. The central element here, a non-consumable tungsten electrode, orchestrates the precise application around delicate materials such as aluminum and stainless steel.
As the late Carl Cockeram, a notable welding engineer once expressed, "Understanding the nuances of welding techniques makes you not just a welder but a creator of structures and dreams." Such wisdom echoes in welding courses offered globally, standing testament to the diverse nature of these techniques.
On another spectrum, we have Flux-Cored Arc Welding (FCAW), similar to MIG but with an added twist of its own flux core. This alternative is celebrated for its efficiency in outdoor settings, triumphing over windy conditions that typically hinder other methods. The built-in shielding allows FCAW to tackle thicker materials with impressive speed.
Technique | Primary Use |
---|---|
SMAW | General Construction, Repairs |
MIG | Automotive, Manufacturing |
TIG | Aerospace, High-End Products |
FCAW | Outdoor Construction, Heavy Work |
The journey through welding techniques unravels endless opportunities. Each method serves as a brushstroke on the canvas of creation, influenced by material characteristics, environmental factors, and the final application's demands. Aspiring welders equipped with a diverse skill set from welding courses are heralded as versatile artists in this ever-evolving craftsmanship, anchoring their success in understanding the intricate details of these renowned techniques.
Tips for Aspiring Welders
Embarking on a journey to become a welder is both exciting and challenging, paving the way to a rewarding career. But, like any craft that requires mastery, welding needs dedication and strategic preparation. If you're just starting out or contemplating whether this is the right path for you, it's essential to focus on building a solid foundation of skills and knowledge. An excellent place to begin is by enrolling in comprehensive welding courses, which offer firsthand experience and in-depth understanding of various welding techniques. Seek programs that provide diverse exposure, from MIG and TIG welding to flux-cored arc welding.
Embrace every learning opportunity, be it in a structured classroom setting or through hands-on workshops. It's equally vital to stay updated with the latest trends and innovations in the welding industry. Follow industry publications, attend workshops, and engage in trade shows to network with professionals and learn from their experiences. While academics and technical skills are crucial, don't overlook the importance of safety, the heartbeat of the welding industry. Familiarize yourself with all safety protocols and invest in quality protective gear. Safety doesn't just protect you; it underscores the integrity of your work.
Apart from technical prowess, physical fitness and stamina are also key factors that can significantly impact your performance and longevity as a welder. The nature of the job requires long hours spent in physically demanding positions, often in less-than-ideal conditions. Regular exercise, focusing on core strength and flexibility, can make your daily tasks more manageable and reduce the risk of injury. Networking within the industry is another invaluable asset. Connecting with other welders can open doors to job opportunities and provide invaluable mentorship. Do not hesitate to reach out to experienced professionals; many are eager to share their knowledge and guide newcomers into the fold.
As you get more comfortable with the craft, explore specialized areas to carve out a niche for yourself. Whether it's underwater welding, pipe fitting, or working in aerospace, having a special skill set can give you an edge in the competitive market. Developing a niche expertise can significantly boost your career prospects and earning potential. Staying curious and open-minded about new challenges will keep you evolving as a professional. A well-rounded approach, combining technical skills, safety consciousness, and physical preparedness, will set you up for success in the inherently demanding but rewarding field of welding.
Quotes and Insights
"Welding isn't just about joining metals; it's about melding art with science. The key to success is staying curious and never stopping learning." — Renowned Welder and Educator, John Doe
Gaining practical experience is crucial, so actively look for apprenticeships or entry-level positions that will allow you to apply your skills in real-world settings. These opportunities not only finesse your skills but also boost your resume, showcasing your hands-on experience to potential employers. By following these strategic steps and continuously embracing new challenges, you can cultivate a strong and fulfilling career in welding. Remember, the path to mastering this craft is an ongoing journey; with each weld you create, you're building your legacy in the world of welding.
Write a comment